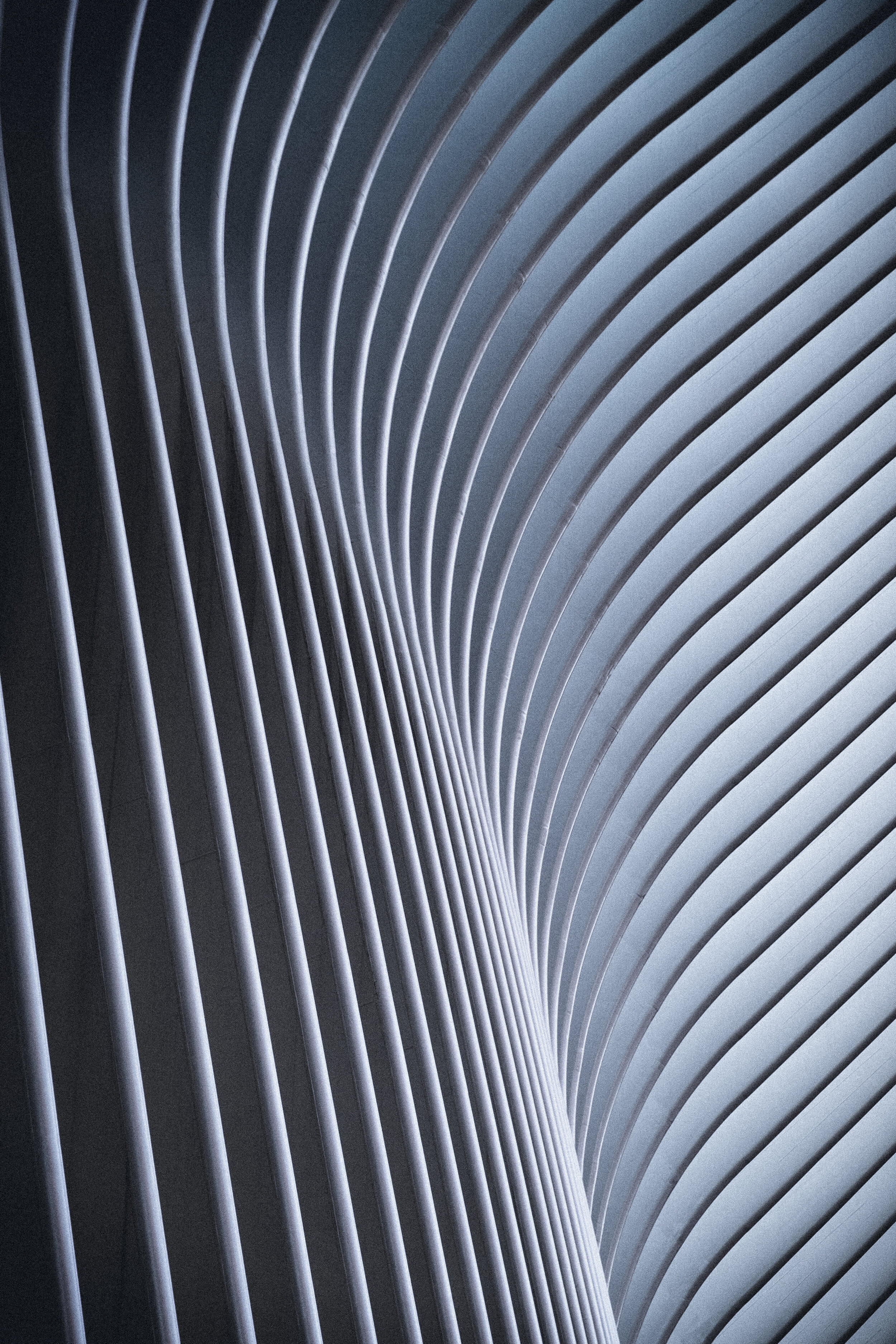
Galvanizing
Dross Removal Pump
Dross Removal
With all maintenance operations conducted on inline process equipment, uptime is paramount. This drives the need for a dross removal system that is fast, agile, and minimizes redistribution of bottom dross. Unlike manual dross operations, bottom dross pumping does not cause redistribution of dross throughout the pot. This means that the pot can be quickly returned to service without waiting for the bottom dross to resettle.
Regular Zinc Pot Maintenance Includes Removing Bottom Dross
Bottom dross is formed when iron and nickel combines with zinc to form heavy dross. While this dross settles to the bottom of the pot (clear of the surface processes) it ultimately displaces clean material in the zinc pot and must be removed. Furthermore - if bottom dross becomes disturbed - it can find its way to the process volume of the zinc pot and introduce hard inclusions, consequently reducing production quality and often leading to time-consuming maintenance with foundry ladles and scrapers.
Features, Benefits, Capabilities
Radical reduction in zinc pot downtime due to routine bottom dross removal operations.
Improved galvanizing process quality with lower suspended inclusions when the zinc pot is returned to service.
Improved overall COO and process availability easily offsets the cost of bottom dross removal pumps and supplies.
Standard Graphite Zinc Transfer Pump
Zinc Transfer Pumps
Zinc transfer pumps can be used for everything from zinc ingot and die casting, to alloying and brass production, continuous galvanizing or emptying hot-dip galvanizing wells for maintenance.