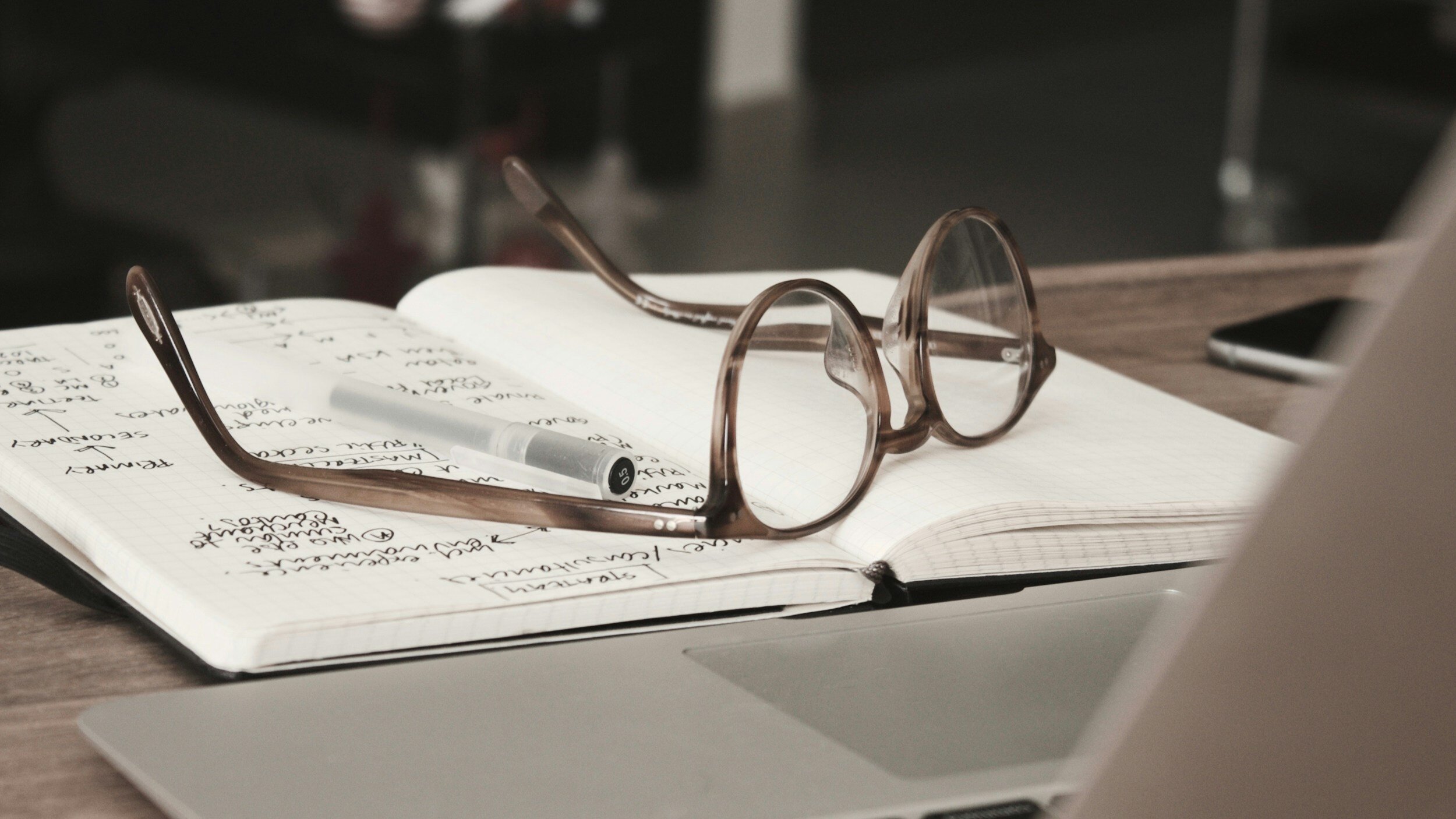
Articles

Cooling Blower Placement and Maintenance for Molten Metal Pump Electric Motors in Foundry Environments
Electric motors operating molten metal pumps in foundry environments face challenging conditions, including high temperatures, dust, and debris. Effective cooling is crucial for motor reliability and longevity. This tech note provides guidelines for blower placement and maintenance to ensure optimal cooling performance in these harsh conditions.

Cover Gas in Secondary Aluminum Melting
In the realm of secondary aluminum melting, refining, and recycling, the utilization of cover gas stands as a pivotal technique for enhancing process efficiency and product quality. Cover gas, essentially an inert gas blanket, serves to shield molten aluminum from the detrimental effects of atmospheric oxygen interaction, mitigating oxidation and dross formation.
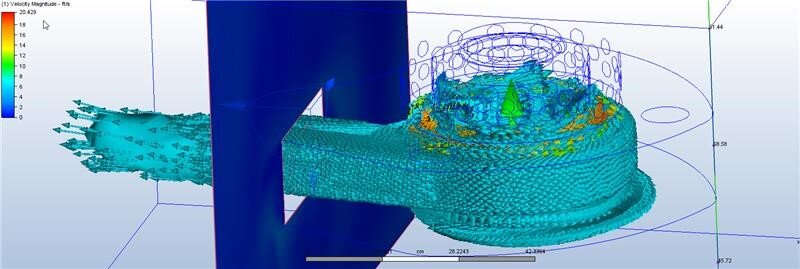
Quantitative Measurements and Characterization: The Key to Optimal Reverberatory Aluminum Melting Furnace Design
Designing an efficient reverberatory aluminum melting furnace is a complex undertaking. It requires careful consideration of various factors that directly affect its performance, energy consumption, and ultimately, your return on investment (ROI). Among these factors, the circulation pump’s sizing, placement, and control play a crucial role. Let’s explore how quantitative measurements and characterization lead to informed decisions in these areas, ensuring optimal furnace system design.
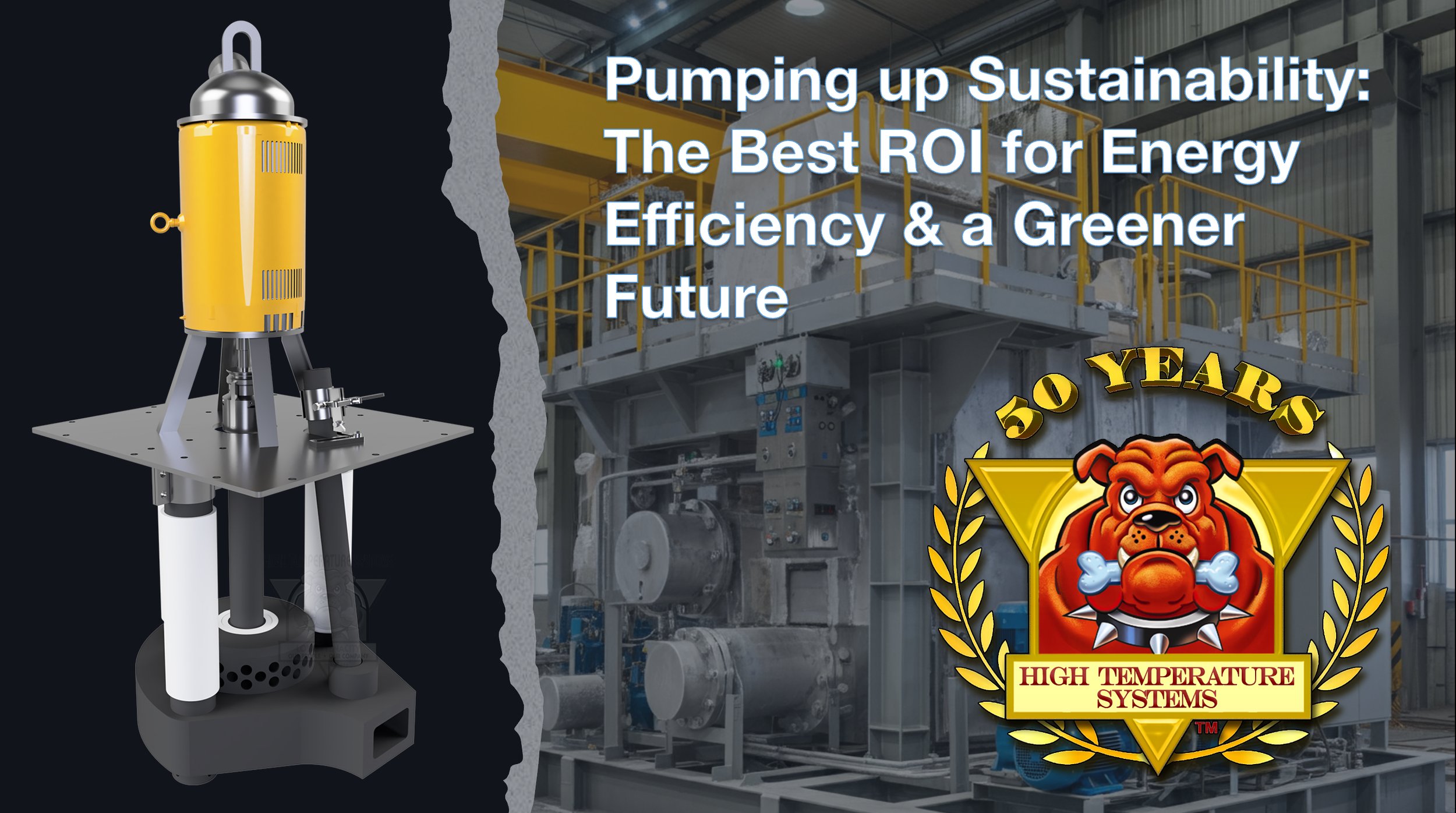
Best ROI for Your Furnace
In the world of aluminum production, achieving optimal energy efficiency and minimizing metal loss isn’t just about cost savings; it’s a critical step towards a greener future. If you’re looking to improve your bottom line and your environmental impact, optimizing your reverberatory aluminum melting furnace is a key strategy. Let’s explore how to maximize your ROI while supporting a more sustainable aluminum industry.
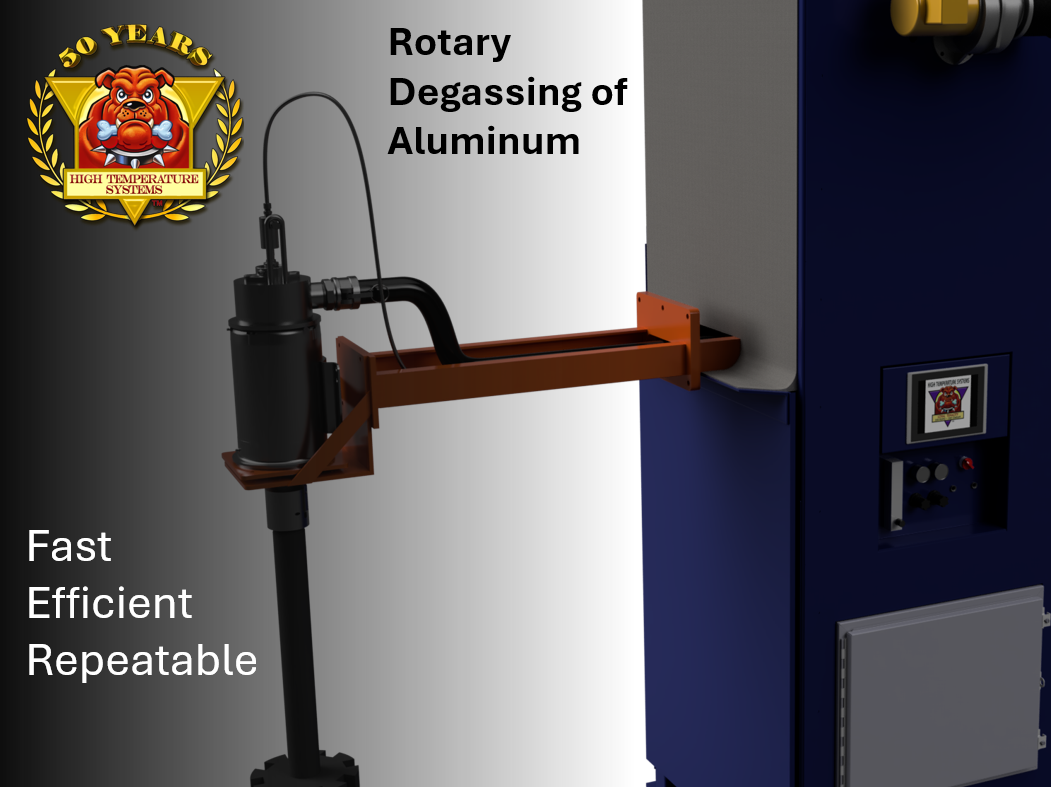
Understanding Rotary Degassing of Aluminum
Rotary degassing is a critical process in aluminum casting to remove dissolved hydrogen and impurities from molten aluminum. Dissolved hydrogen, if left unchecked, forms bubbles during solidification, leading to porosity in the final casting. This porosity negatively affects mechanical properties, reducing strength and ductility.
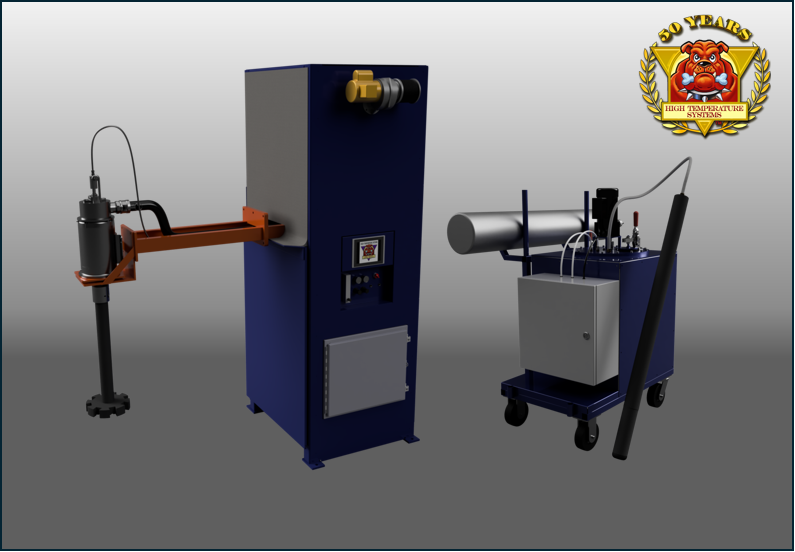
Aluminum Degassing Methods - Picking the Best Method
There are six commonly recognized methods of degassing aluminum. These are briefly discussed below along with the pros and cons of each method.
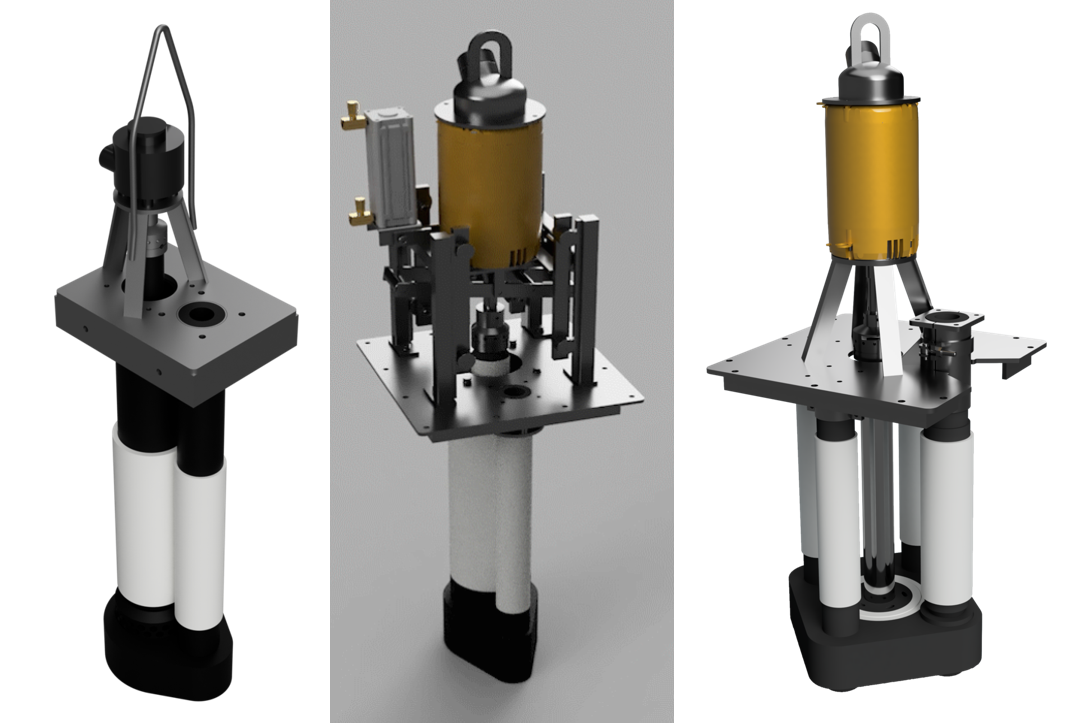
Transfer Pump Types
Closed, Dual Position, and Open Style transfer pumps are available in a range of sizes to accommodate any applications.
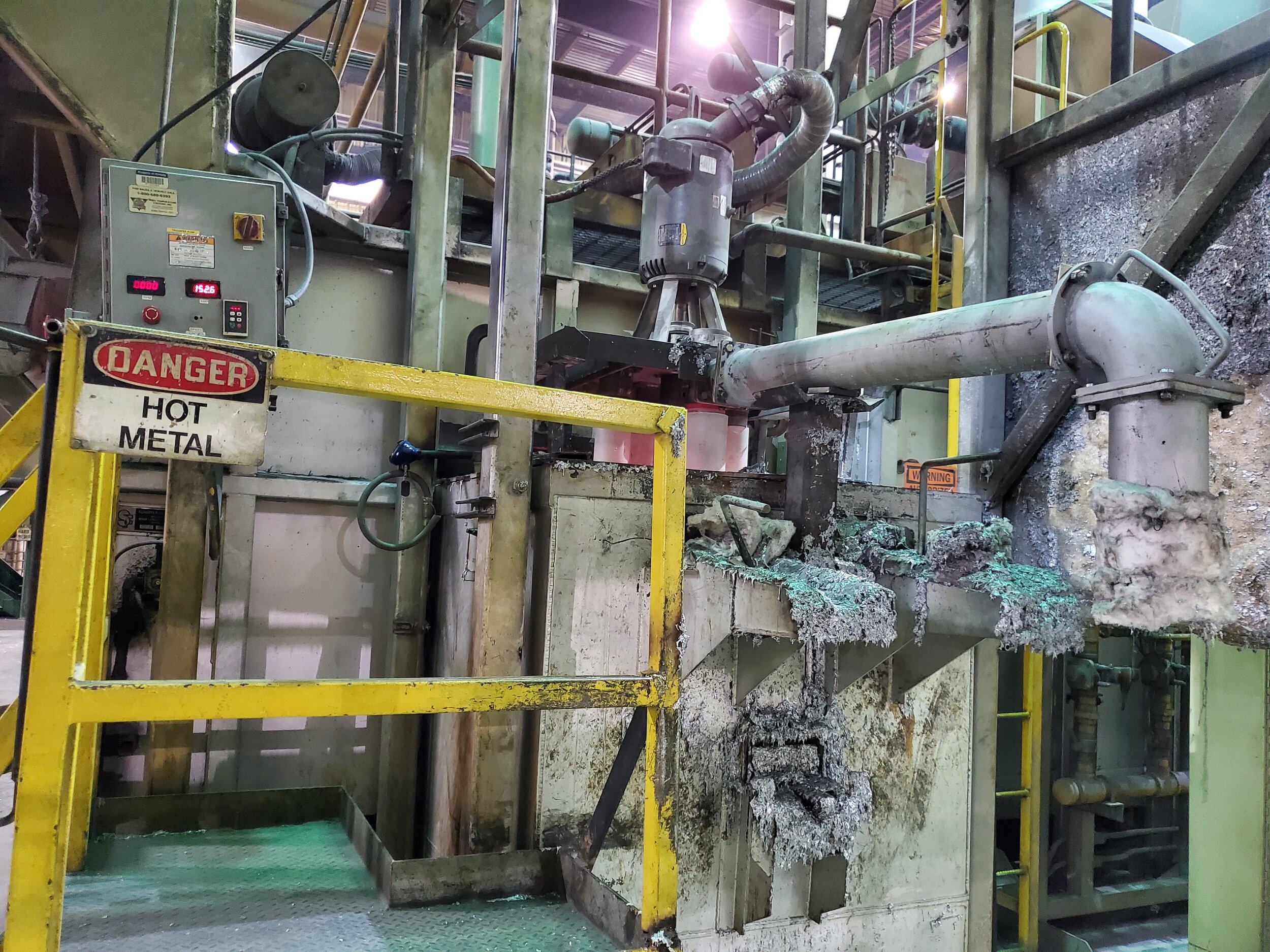
Intelligent Control for the Smart Foundry
Nearing the quarter of the 21st century, it seems technology is advancing faster and faster every year. Why shouldn’t your facility advance too? This post will provide some options for you to consider as you’re researching, designing, and improving your process.
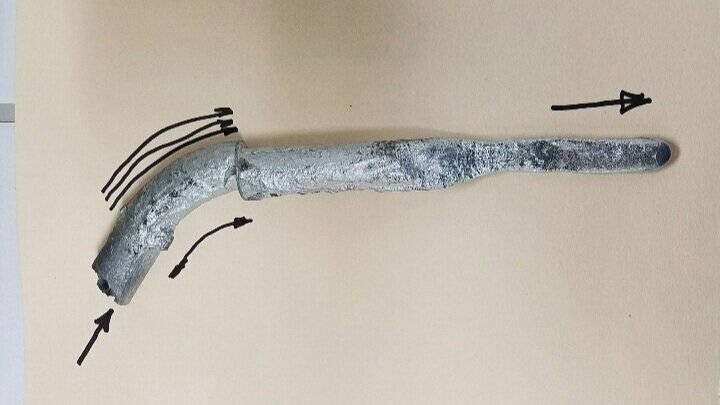
Low Air Flow Freezes Pumps!
The primary reason for molten metal pump freezing is "slow starts." A slow-start is defined as slowly increasing the motor RPM. When a transfer pump is slow-started, the hot metal flows gradually into a cooler riser. As the metal temperature decreases, it solidifies or freezes inside the riser. This slow-start condition typically results in permanent damage and the need to rebuild the pump or at the very least replace the riser.
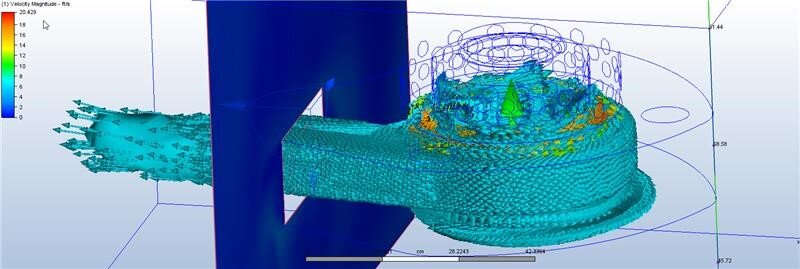
Expertly Optimized Solutions
High Temperature Systems, Inc. partners with melt department managers, supervisors, and engineers to craft complete solutions and solve problems that are beyond the reach of industry off-the-shelf solutions. Drawing from our standard product lines and more than 50 years of experience, we can craft solutions unique to your applications and furnace implementations. These solutions encompass aluminum, zinc and lead operations from die casting to galvanizing.
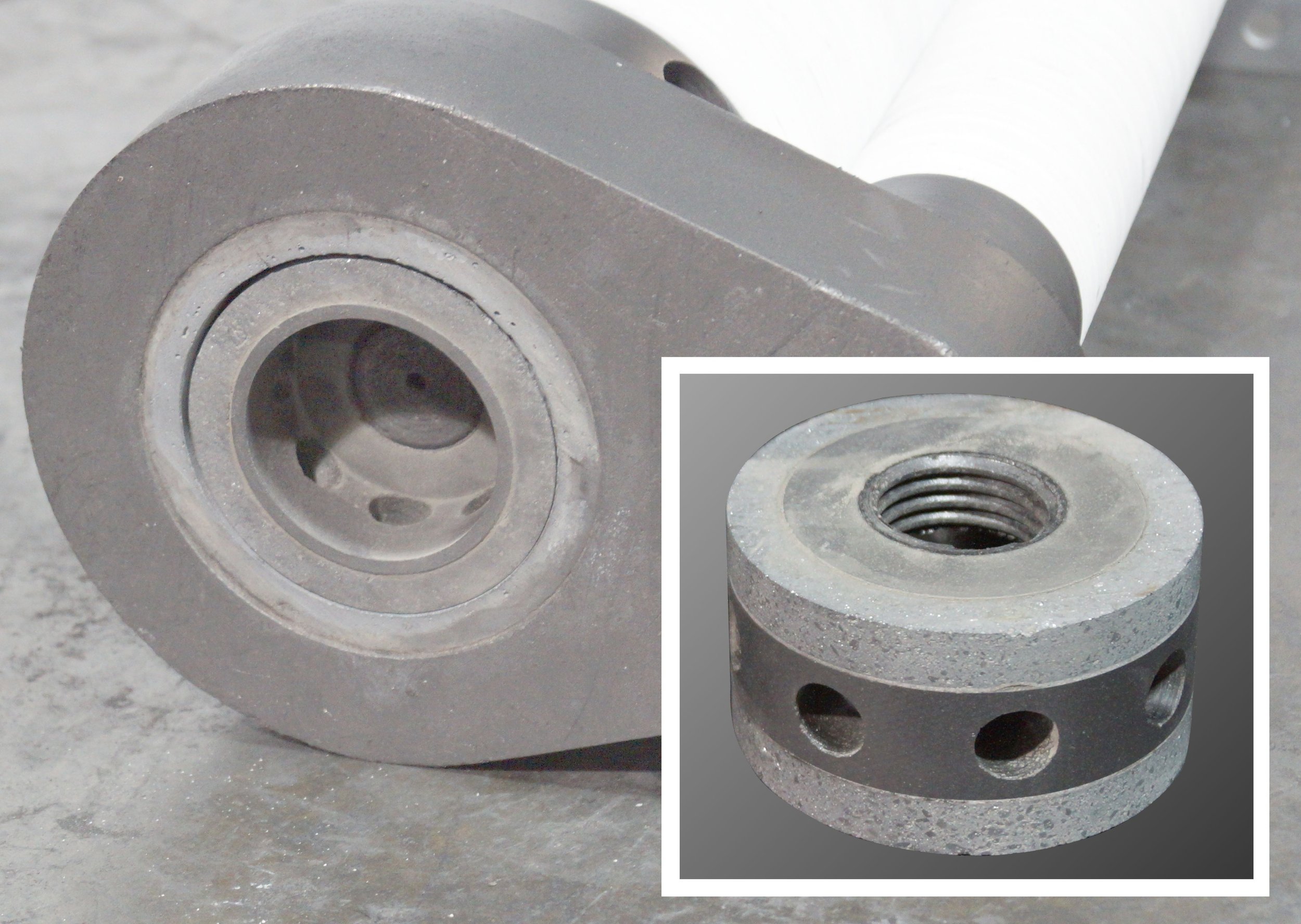
Impeller Types and Purposes
We offer three different types of impellers for many of our molten metal pumps. (The impeller is the vaned wheel that spins inside the pump base.) The impeller and its interaction with the pump base (and base volute) largely determine the performance characteristics of a given pump design.
Circulate Continuously - Transfer on Demand
The ideal solution for these furnaces would be a single compact pump that performs both the circulation function and the transfer function. Such a pump would require a mechanism to redirect the output of the pump impeller to either a circulation nozzle or a transfer riser.

Pump Installation Planning Guidelines – Part 2 – Pump Startup Scheduling
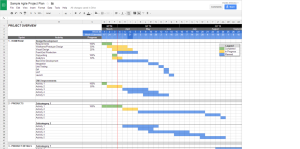
Pump Installation Planning Guidelines - Part 1 - Start at 40,000 ft!
Air Supply Considerations for an Air Motor on a Molten Metal Pump
Graphite - Non-Wetting in Molten Zinc
3-Phase Motor Running Backwards?
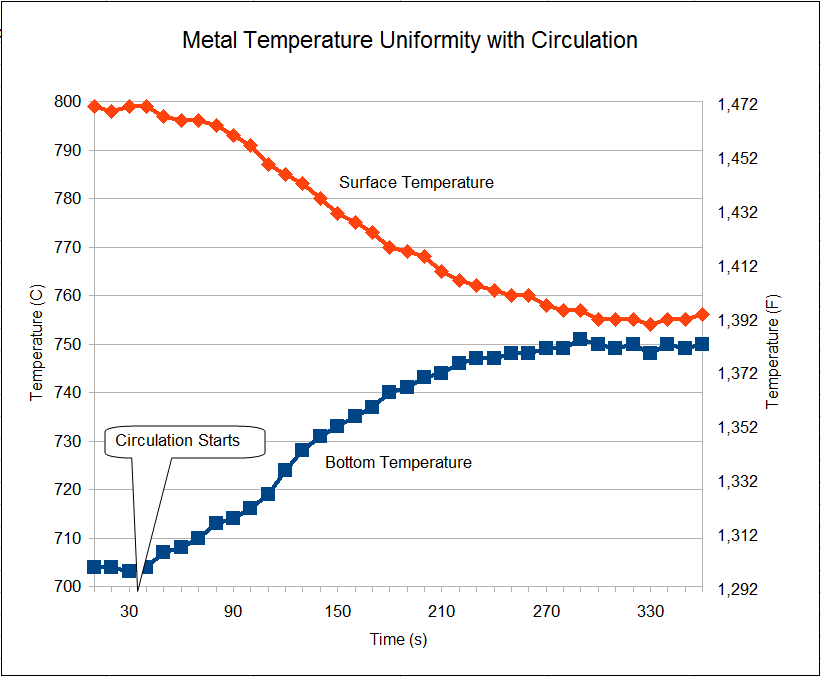
Why Should I Use a Circulation Pump?
In most real world applications, any one of these benefits results in savings that more than offsets the cost of a circulation pump. As an example, a properly sized and operated circulation pump can increase overall furnace throughput 15% and in some cases 30% for a small fraction of the cost of a furnace expansion project.