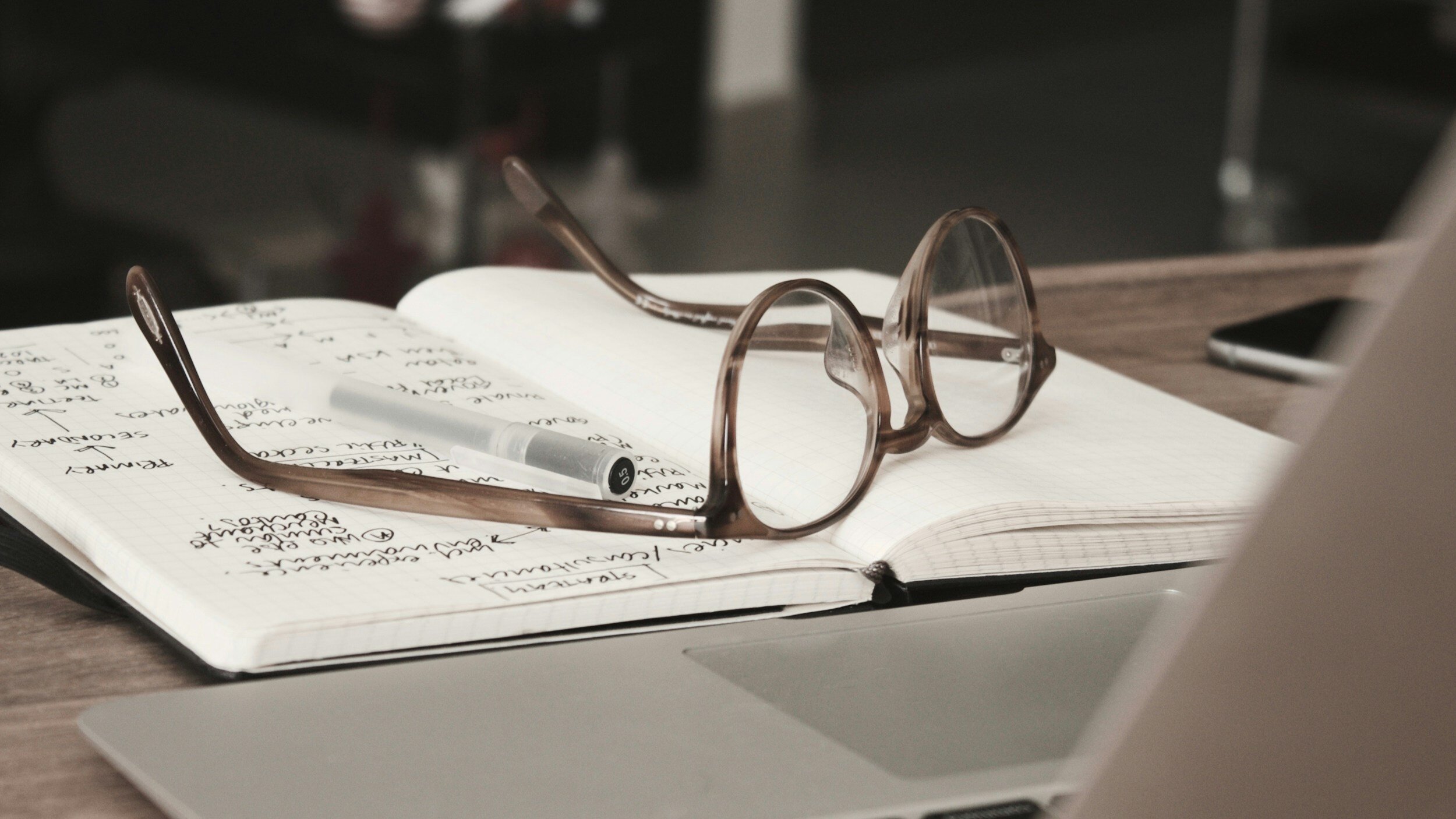
Articles

Cover Gas in Secondary Aluminum Melting
In the realm of secondary aluminum melting, refining, and recycling, the utilization of cover gas stands as a pivotal technique for enhancing process efficiency and product quality. Cover gas, essentially an inert gas blanket, serves to shield molten aluminum from the detrimental effects of atmospheric oxygen interaction, mitigating oxidation and dross formation.
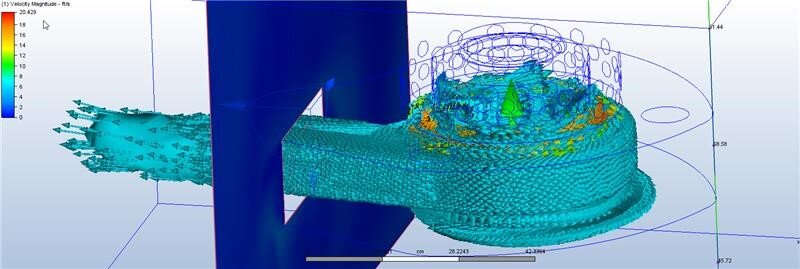
Quantitative Measurements and Characterization: The Key to Optimal Reverberatory Aluminum Melting Furnace Design
Designing an efficient reverberatory aluminum melting furnace is a complex undertaking. It requires careful consideration of various factors that directly affect its performance, energy consumption, and ultimately, your return on investment (ROI). Among these factors, the circulation pump’s sizing, placement, and control play a crucial role. Let’s explore how quantitative measurements and characterization lead to informed decisions in these areas, ensuring optimal furnace system design.
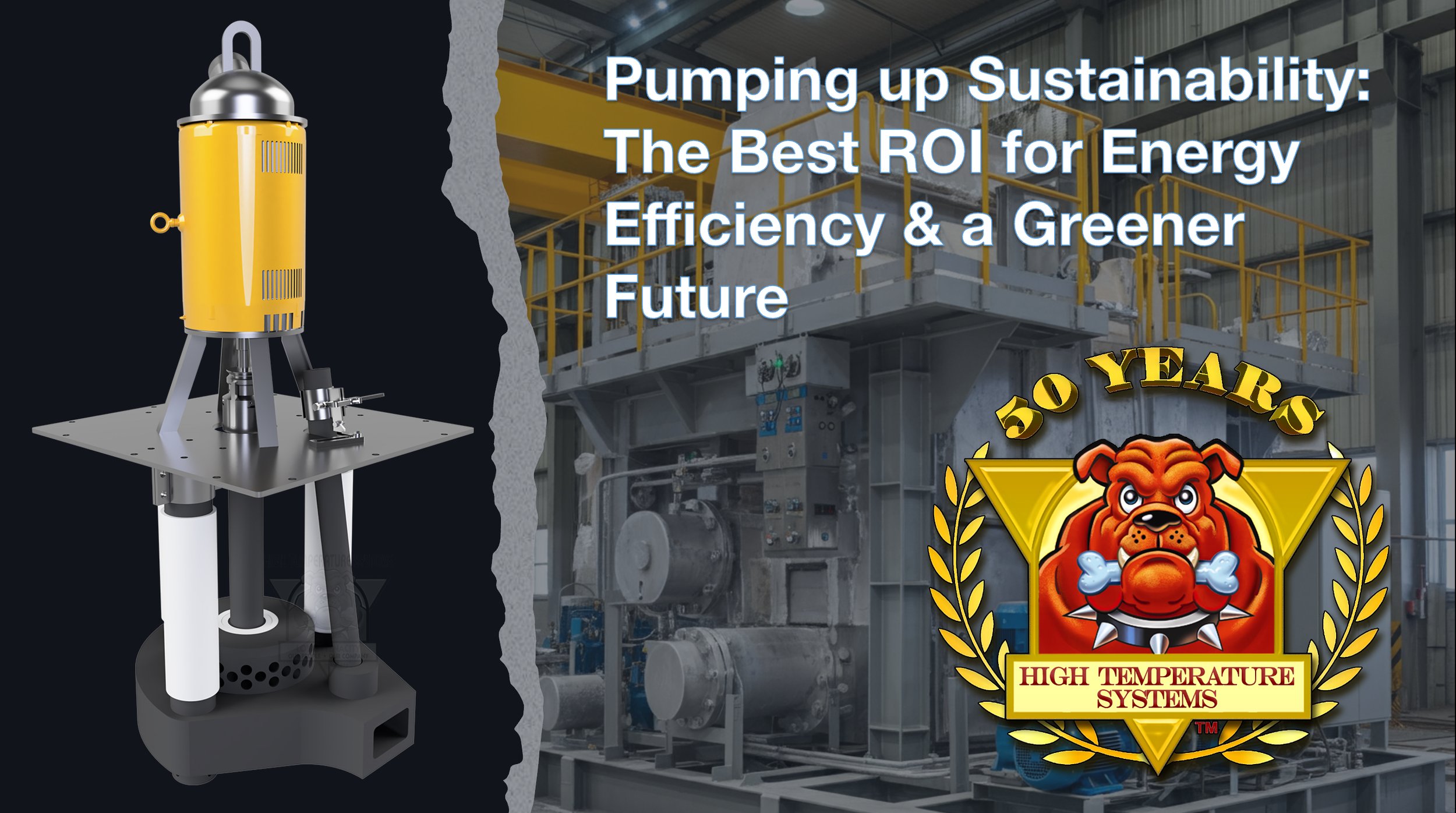
Best ROI for Your Furnace
In the world of aluminum production, achieving optimal energy efficiency and minimizing metal loss isn’t just about cost savings; it’s a critical step towards a greener future. If you’re looking to improve your bottom line and your environmental impact, optimizing your reverberatory aluminum melting furnace is a key strategy. Let’s explore how to maximize your ROI while supporting a more sustainable aluminum industry.
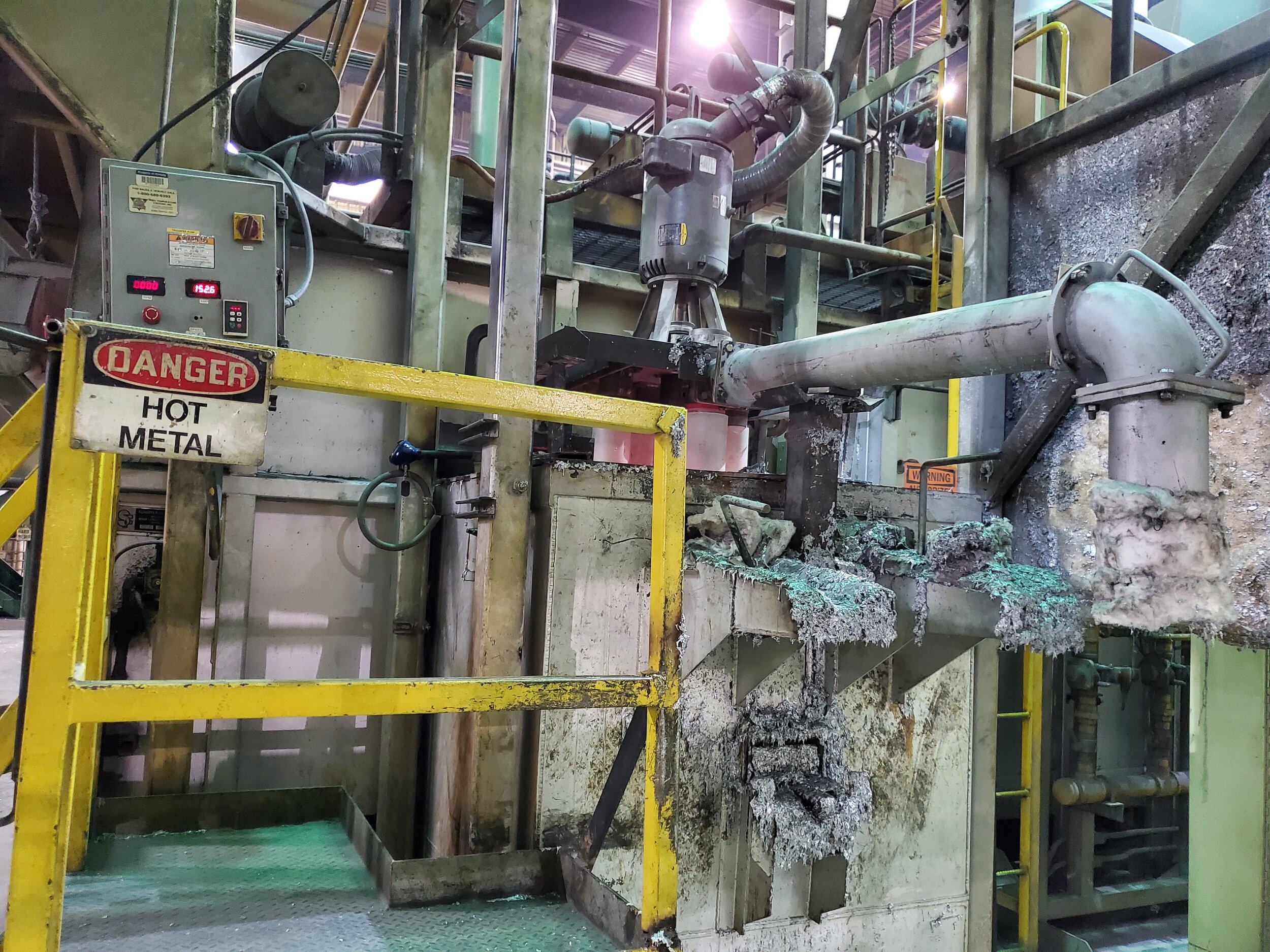
Intelligent Control for the Smart Foundry
Nearing the quarter of the 21st century, it seems technology is advancing faster and faster every year. Why shouldn’t your facility advance too? This post will provide some options for you to consider as you’re researching, designing, and improving your process.